Optex Manufacturing (Design Process)
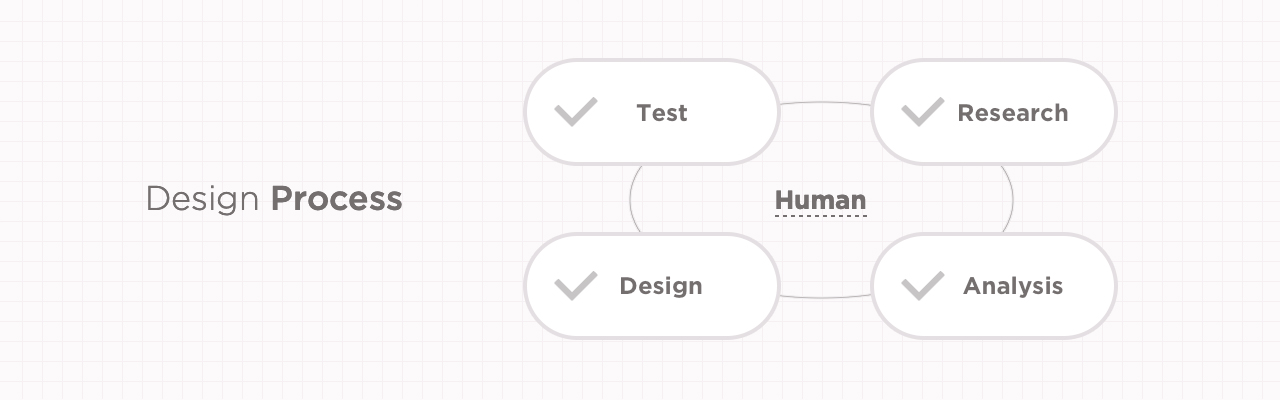
Design Process
At Optex, we strive to produce products that are both unique and also loved and used for a long time.
Our approach to manufacturing is Human-Centered Design (HCD), which considers the perspective of a wide range of customers that use our products.
1: (Research) Understanding How the Products Will Be Used, and By Who
[Research]
Our development and sales teams join forces, and visit places around the world where our products are installed. They check who are using our products, and in what situations and ways, and listen to what our customers have to say.
This is how we are able to get a clear picture of our customers’ circumstances and what’s happening at installation and usage sites, and start searching for what it is that will provide our customers with what they truly need.
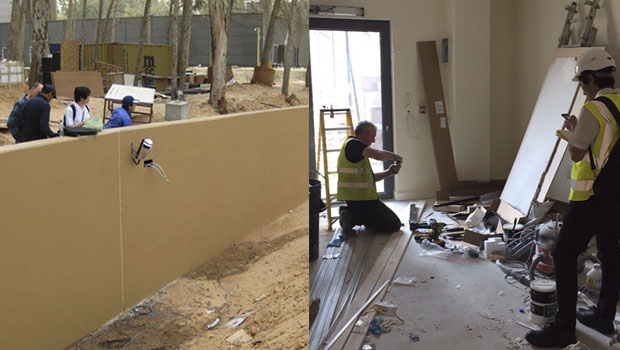
2: (Analysis) Clarifying Customers’ Issues and Needs
[Customer Journey Map]
We try to understand and visualize the type of emotions and actions our customers will have at each phase of becoming aware of, selecting and eventually using Optex products. This enables us to identify any issues our customers may have, and for our employees to develop a shared awareness of each customer’s situation.
[New Product Planning Sheet]
We use this sheet in the product development process to clarify and organize information on the quality our customers require, and the value we will offer them.
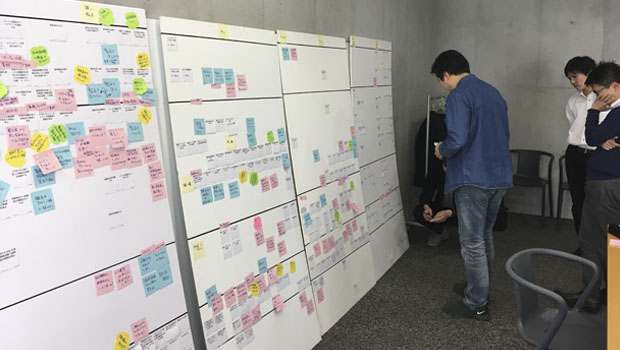
3: (Design) Specifying Possible Solutions Using Prototyping
[Prototyping]
By creating a series of prototypes of our designs, we are able to get an objective and more thorough idea of what we want to create. Repeating this cycle of setting up a hypothesis and verifying it is how we achieve even better manufacturing.
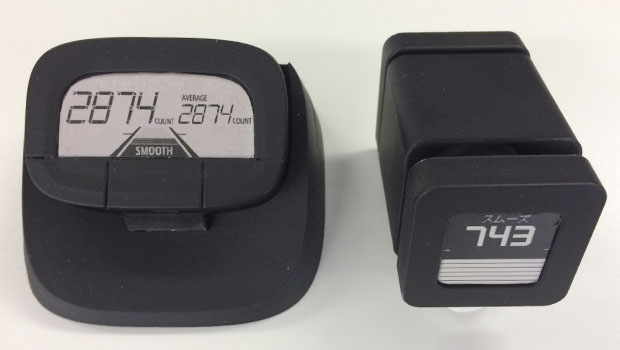
4: (Test) Evaluating the Design Against its Requirements
[Usability Tests]
We use employees as test subjects (acting as customers), and run tests to identify aspects of the product that are difficult to use or understand, and check if it is really what the customer requires while evaluating how the product is explained and operated when it is actually installed.
These tests are carried out by developers, salespersons and other relevant employees, and the quantitative and qualitative results are analyzed and shared with the product development team.
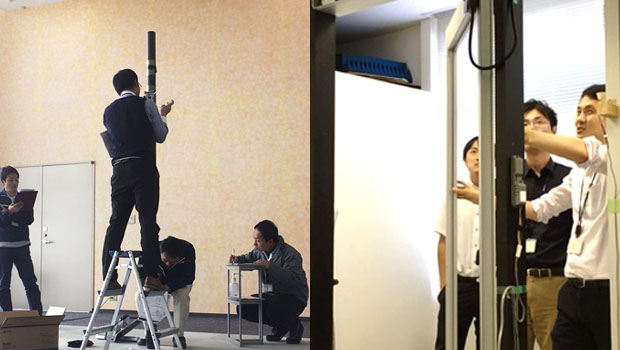
Meetings and the Good Design Award
[Reinventing Meetings (Huddle Meeting)]
Developing products with a shared vision and preferences requires open communication that allows for a lively discussion of ideas. The Optex Meeting Cube is an original item we developed in a design project to facilitate such communication.
[Aiming for the Good Design Award]
We have set our sights on winning the Good Design Award, which is an opportunity for our designs to be objectively appraised by a panel of experts, and a way for the Optex approach to manufacturing to be more widely known in society.
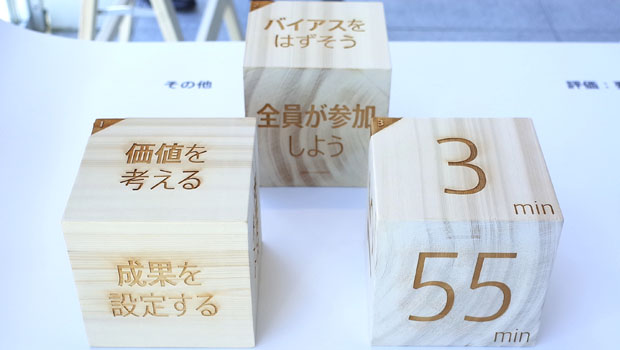
Contact phone number
- Headquarters
- +81-77-579-8000
Contact form